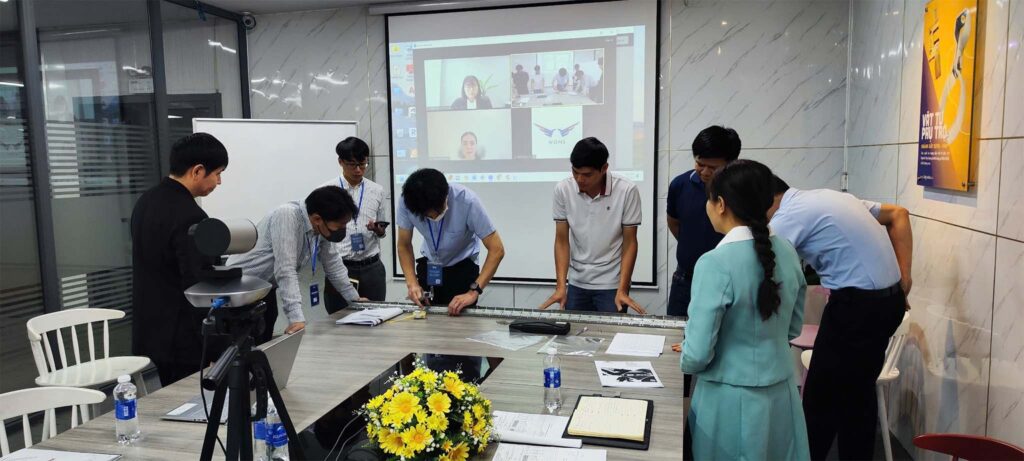
目次
お客様からBizmatchへのご依頼相談内容
製造業務向け加工部品の販売を手がけるG社からベトナム国内の製造工場とタイアップをして、強度の高いユニストラットの共同開発・製造・販売をしたいと依頼を受けました。
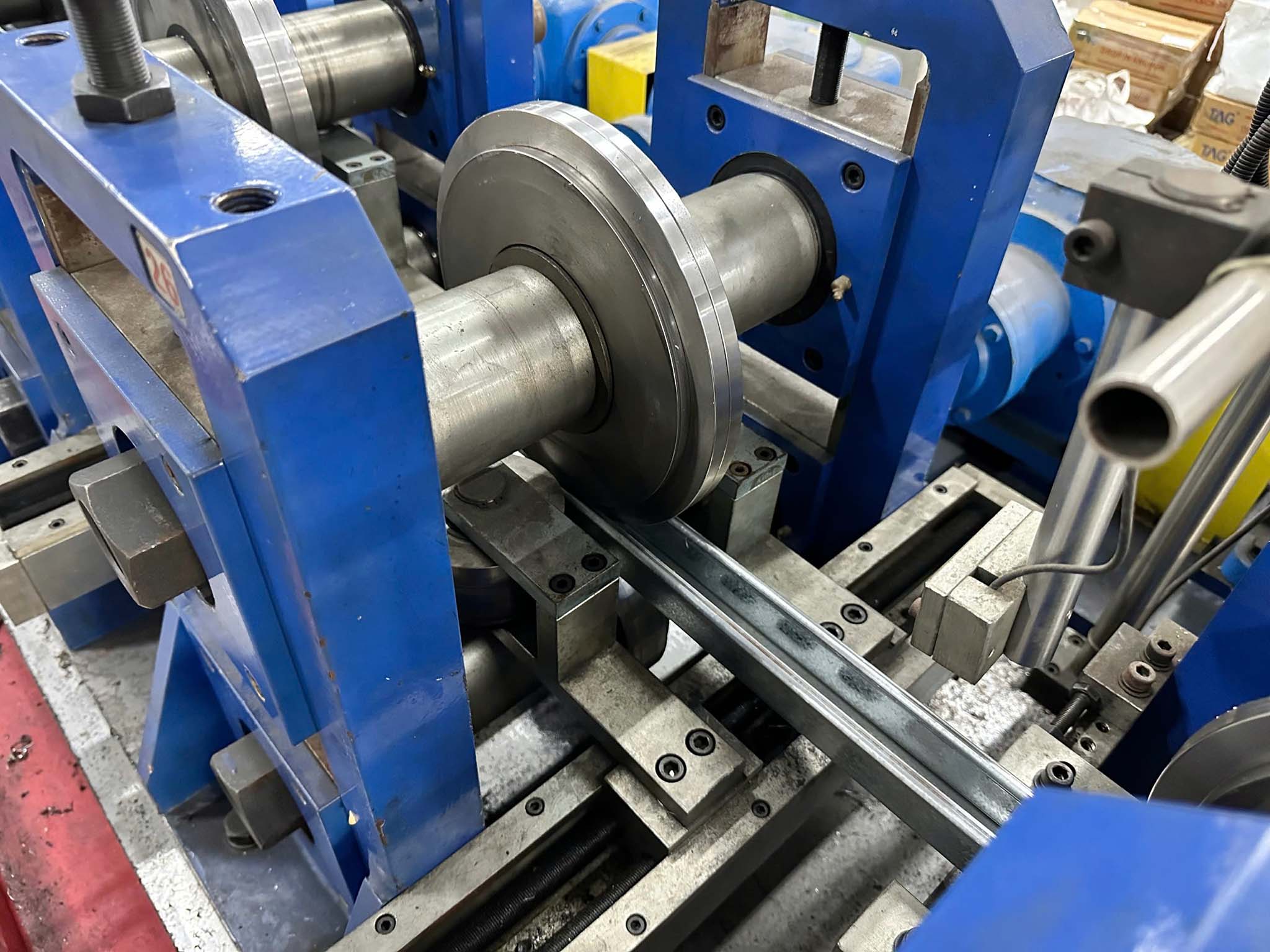
ユニストラットは工場の設備工事で電気ケーブル、導管、およびパイプをサポートおよび固定するために一般的に使用されますが、日本市場には軽量で強度の弱い製品しかなく、大型工場の設備環境に耐えうる最適な製品が存在していないことからの要望でした。
プロジェクトの目標
日本市場で流通しているユニストラット製品よりも材質も品質も高い製品を希望価格内で調達できる海外ルートを開拓して、日本国内でメーカーとしての地位を確立させることを目標設定しました。
プロジェクト進行の流れ
ステップ1: 依頼主(G社)のニーズ整理と製品知識の研究と調査
ユニストラットの用途はすぐに理解できましたが、ベトナム国内で製造・流通されている商品は日本製品と比較すると公差や仕上げの見た目の重要性が低いため、日本の基準と品質で製造できる工場が少ない状況でしたが、本プロジェクトの可能性にビジネスチャンスを感じてもらえたベトナム企業をG社へ5社リストアップいたしました。
ステップ2: 工場視察アテンド・ベトナム経営層との意見交換の実施
G社とウォンズベトナムスタッフは、訪問前に見積もりや輸送価格などを含めて、協議を重ねてリストアップ企業の中から最も条件に見合う企業を選定し、工場の視察アテンドとベトナム企業側の社長、営業部長、工場長、製造スタッフによる合同会議にて意見交換会を開催しました。
ステップ3: ベトナム企業との契約交渉と契約書作成・締結サポートの実施
ウォンズベトナム担当者は、複数回に渡るサンプル品の製造について、無料製造の条件交渉を成立させ、日本基準と品質をクリアするサンプル品の完成をサポートいたしました。 続いてウォンズ日本・ベトナムの両チームメンバーは、ベトナム企業と計10回以上の契約交渉を重ねて、両企業が譲歩できる契約条件の交渉成立と契約締結の調印式開催までサポートを実施しました。
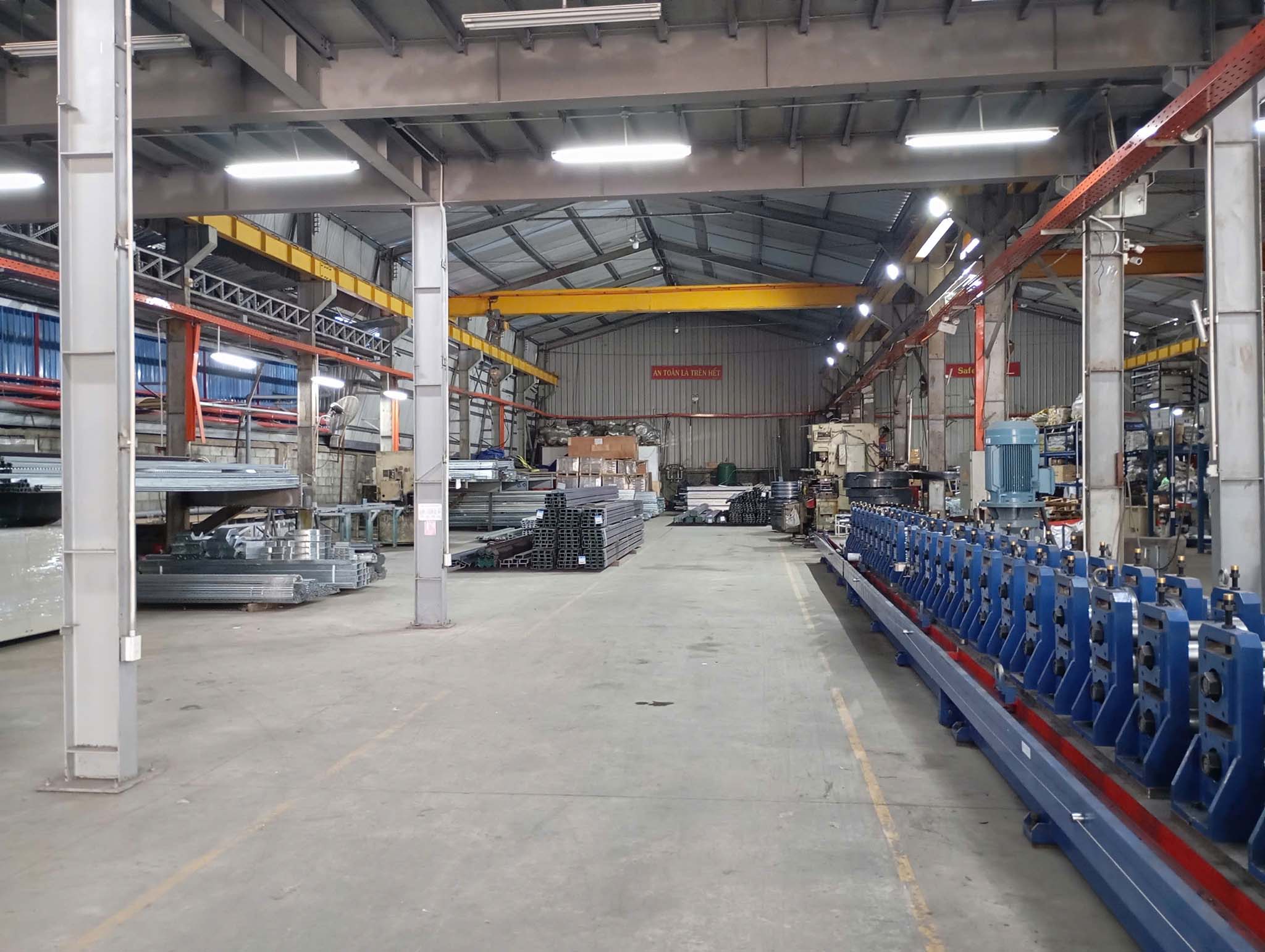
ステップ4: オンライン製造テストによる品質改良とオンライン検品の実施
サンプル品から実際の大量生産に入る過程において品質劣化や不良品の発生を防ぐために、日本とベトナムをオンラインビデオで接続し、製造テストを繰り返しました。
実際の製造過程のチェックや完成した製本の品質基準の抜き打ちチェックを数回にわけて提案・サポートいたしました。大量生産中に公差の許容を超えてしまうケースが発生し、製造工程の見直しに取り組んでいただきました。
ベトナム企業側に根気よく基準と工程のルールを説明し、大量生産ながら不良品率0%を実現させることができました。
また合わせて、ベトナム企業には抜き打ちの検品テストにもご協力いただきました。
ステップ5: 製品梱包ならびに輸送サポートの実施
ウォンズベトナムが特に注意していることが、輸送時の梱包状態です。梱包段階でG社から船荷輸送時の対策として、防錆塗装の相談があり、ベトナム企業側と対策を進めました。
せっかく製造の品質基準をクリアしても、輸送時に錆びたり、傷がついたりしては台無しになります。梱包状態についても、商品の特性を考えた丁寧なビニール包装に加えて、木箱への梱包方法を輸送費コストが上がらない梱包形態を製造会社と輸送会社と検討と協力をしていただきました。
ベトナム企業が日本への輸出実績がなかったため、ウォンズスタッフにてベトナム国内における輸送会社の手配、荷受けの中間サポート、書類準備サポートなどきめ細やかなサービスを提供し、無事に日本で製品をお届けすることができました。
プロジェクトの成果
プロジェクトの目標であった日本市場で流通しているユニストラット製品よりも材質も品質も高い製品を希望価格内で調達できる海外ルートを開拓できたことは大きな成果でした。
本製品は、日本で注目されている某大型工場に納品され、問題なく活用されたことで達成感があります。
G社はこの実績をもとに追加受注を獲得できたと報告をいただけたことは大変嬉しかったです。
ベトナムスタッフが大変だったこと
本プロジェクトで、一番大きな課題は、ベトナムと日本のユニストラット製品で求められる基準と品質のギャップでした。
ベトナム市場におけるユニストラットは公差や表面品質の粗さは傷や歪みなどが許容されるため、日本市場で流通しているユニストラット製品よりも材質も品質も高い製品を希望価格内で製造開発協力をしてくれるベトナム企業を探すことは大変でした。
契約交渉については、両社にとってチャレンジングなプロジェクトでしたので、信頼関係が築かれていない状態で、不確実性の責任分岐点や条件交渉のサポートについて、日越ウォンズスタッフは非常にタフな交渉が多く求められたため大変苦労しました。
ベトナムスタッフが工夫したこと
ベトナムにおける製造工程では、G社の図面と仕様書で示された公差と表面をクリアするユニストラットの製造機械を保有する企業は少なく、また長さがある商品ですので、大量生産中に徐々に歪みが生じるため随時油断せず、検品と調整を繰り返す必要がありました。
両国各社担当者を交えてオンライン意見交換会の開催、現地での製造テスト、オンライン検品の計画など、不良品を発生させない取り組みについて、両社の意見をまとめて調整したできたことは、ベトナムスタッフの経験のおかげで工夫できたことだと考えます。
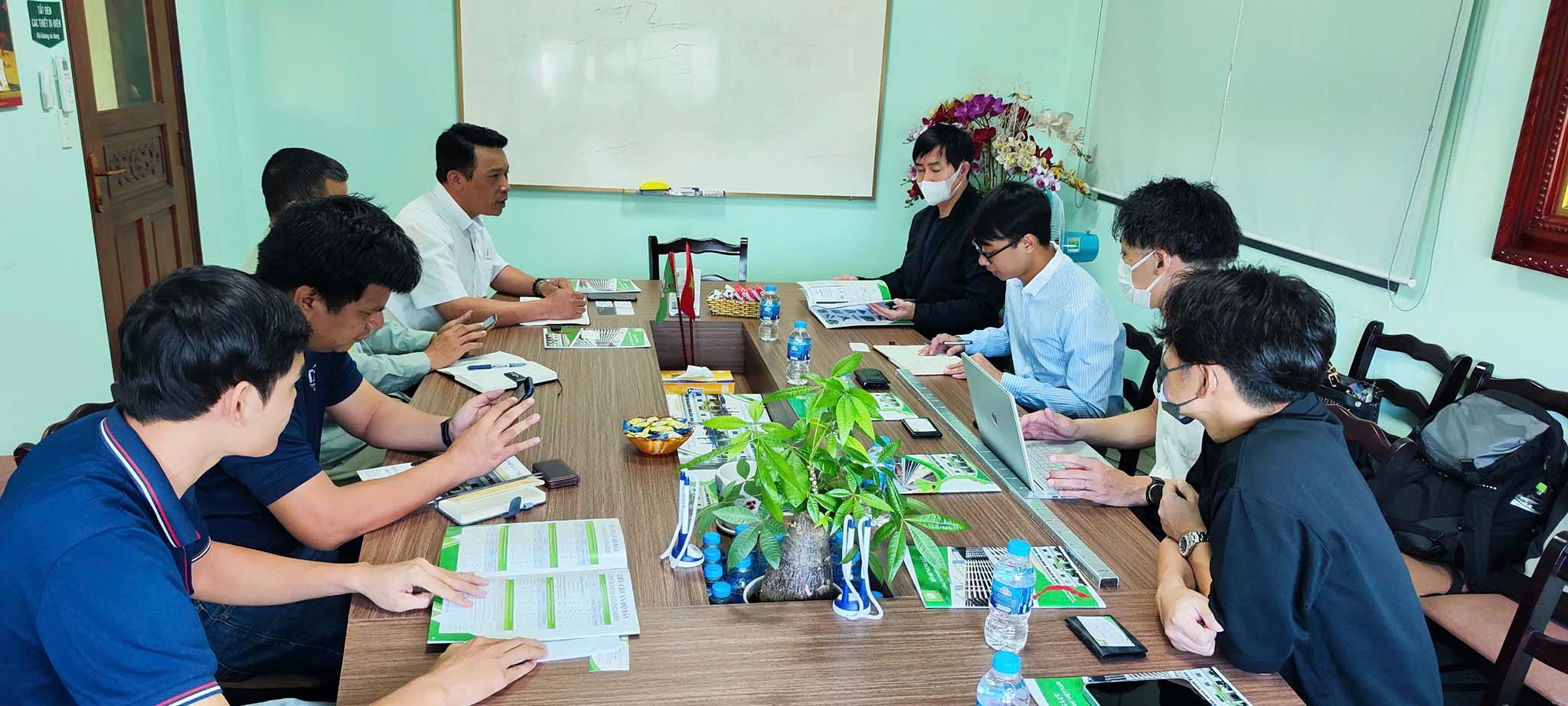
日本スタッフが大変だったこと
今回、G社とベトナム企業との間で製品に対するクオリティーの考え方の違いを合わせることが大変でした。製造を依頼したベトナム企業は工場も広く、機械も充実していましたが海外との取引回数が少ない企業でした。そのため、日本の製品に対するクオリティーを理解できておらず、両社の意見を一致させるところからのスタートでした。
ユニストラットは幾つかの種類があり、今回、G社が注文を希望された製品は6mmの長さのある横に長い製品でした。
G社がベトナム企業を訪問した際、ベトナム企業ではサンプル品を準備をしてくれていたのですが、本来は真っ直ぐに伸びた6mmの製品でしたが途中にたわみがあり、製品のレール部分の曲げの角度が違っていた箇所もありました。
ベトナムではこのクオリティーで利用されていましたが、日本のクオリティーは図面に忠実な製品を求められます。
G社からの要望をベトナム企業に伝え、ベトナム企業はその日の内に工場で調整をしてくれました。その後、試行錯誤をし日本の品質レベルまで作り上げることができました。
さらに、G社からより日本の品質レベルまで達しているかを確認するためにベトナムで許容荷重検査をすることになりました。当初、ベトナム企業は協力的ではありませんでしたが、日本のクオリティーの重要性、G社は安全第一である製品を希望されていることをベトナム企業へ伝え、ベトナム国家に属した品質保証試験センターで耐久検査をし品質に問題ないことが証明されました。
日本とベトナムでの考え方、やり方には大きな違いがあるため、両社の意見を合わせながらプロジェクトを進めるのは大変ですが、製品が出来上がり、日本のG社に製品が届いた際は、両社とも信頼関係が増し、次の発注に繋げることができました。
日本スタッフが工夫したこと
ユニストラットにはいくつものサイズや形状があり、加工方法や塗装についてもいくつか種類があります。今回、注文時にG社とベトナム企業との間でサイズの認識違いがおきました。
発注までの流れですが、まずは希望する製品の見積価格をベトナム企業へ連絡し確認をとります。その後、企業規模や製品価格を確認し、直接G社がベトナムへ訪問されサンプル品をチェックします。その後、G社は正式に注文をベトナム企業へ依頼しますが、企業調査を含み、それまでの間に6ヶ月〜8ヶ月ほどかかります。その間、いくつもの図面、見積書、そのほか書類のやり取りが続きます。そのため、G社とベトナム企業との間で情報の整理がつかず、注文の時点でサイズについて両社の意見に食い違いがありました。
私たちはこれまでのやり取りデータを全て見直し、会社ごとに日付順で図面、見積書、注文書、契約書、そのほか重要な書類をフォルダーで分け、G社がいつでも過去のデータを見直すことができるクラウドのデータフォルダーを作成しました。そのデータフォルダーはG社の担当スタッフが過去の資料から最新のデータまでいつでも確認することができます。
このデータフォルダができたことで、G社とベトナム企業のやり取りで両社の認識のずれがなくなり、さらにはG社にとって今後データを活用して営業ができるスキームを構築できました。
プロジェクトリーダーの総合評価
ベトナムでは業種関わらず、個別にサンプル品を製造することと、大量生産中に品質劣化や不良品の発生率が高くなるトラブルは起こりやすいです。
そういったトラブルを耳にすることが多いため、私たちウォンズスタッフの『Bizmatch』サービスでは、特に取引の最初の段階に、そういったトラブルが発生しないよう両社に働きかけるようにしていますが、今回も日本とベトナムの両企業にとってプロジェクトの成功体験を導き出す一翼をウォンズスタッフは無事に担えたと、誇りに感じています。